
Low-voltage electrical terminals of electrical appliances: key components for stable connection
Unlock the Secrets of Safe and Reliable Power Transmission
When we talk about low-voltage electrical terminals of electrical appliances, this is not just a simple contact point between two metal pieces. In fact, they are a vital part of the entire power system, responsible for ensuring the smooth conduction of current and protecting the line from damage. Precise design coupled with the use of high quality materials allows these small devices to perform well in complex environments.
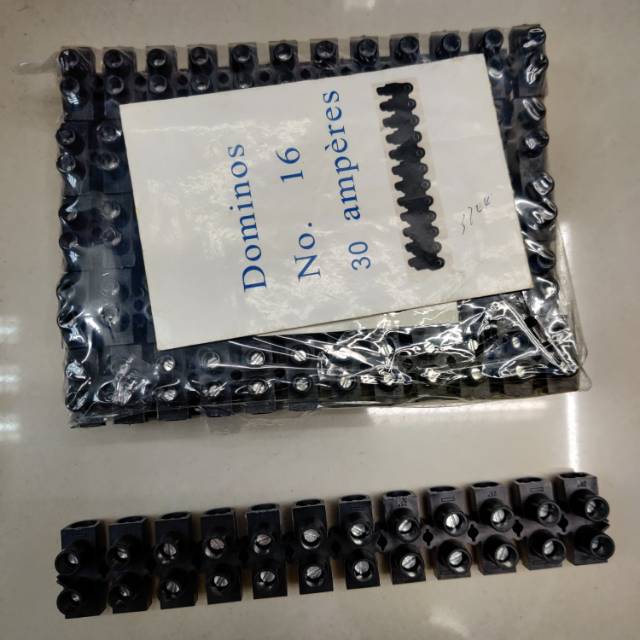
Well-designed electrical terminal structure
By introducing an efficient heat dissipation mechanism and high-temperature insulation, low-voltage electrical terminals can effectively prevent short circuits, overloads and other problems, greatly improving the safety and stability of the system. Whether it is on the high-power motors that work continuously in the factory workshop or next to the microprocessor chips in the smart home, you can see them working silently.
From Industry to Home: Ubiquitous Applications
The application range of low-voltage electrical terminals is extremely wide, covering almost all places involving power distribution. On the manufacturing assembly line, it ensures the energy supply required for the precise movement of the robot arm; on the construction site of high-rise buildings, it is used to connect the wire network between temporary lighting facilities and power outlets. Not only that, the communication base station also relies on this device to manage the power supply of the signal amplifier to ensure that the mobile phone calls are unimpeded.
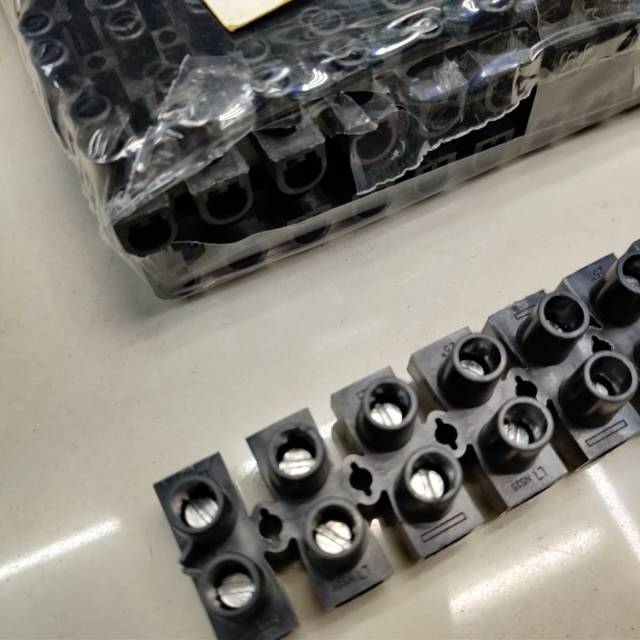
Typical application examples in different fields
For ordinary home users, although they can't see the complicated wiring projects hidden behind the trunking, the TV, refrigerator and even charging treasure they use every day cannot do without the support of this behind-the-scenes hero. It can be said that it is the existence of these seemingly inconspicuous small parts that make the convenience of modern life possible.
Picking the Right Partner: The Art of Engineer Selection
In the face of a wide range of low-voltage electrical terminal products, how to make a wise choice has become the task in front of each technician. First of all, the special requirements of specific projects must be clarified, including the expected load size, working environment conditions and other factors. Then, based on the above considerations, the indicators of the required model are determined-such as material type (copper plated silver vs stainless steel), rated voltage level (DC/AC) and wiring mode, etc.
For example, when installing a video surveillance camera in an outdoor humid environment, it is particularly important to give priority to stainless steel products with good anti-corrosion performance; and for automobile engine controller modules running under high-frequency vibration conditions, it is necessary to use Crimping type with strong vibration resistance to ensure firm and reliable connection.
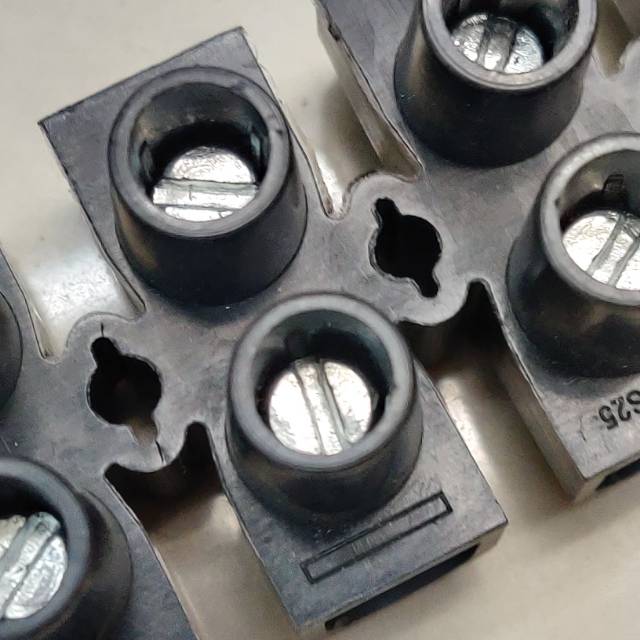
Comparison of the characteristics of different types of low-voltage electrical terminals
Quality first: the standard for achieving excellent performance
Excellent quality is always one of the most basic and important criteria to measure the quality of a commodity. In order to create satisfactory low-voltage electrical terminals, manufacturers usually formulate a series of strict technical specifications and strictly implement the operating procedures of each production process. Starting from the source to control the source of raw materials, only select the base materials provided by reputable suppliers that meet the international certification specifications; Then complete the high-precision cutting process with the help of advanced numerical control machine tools; Finally, it has to go through several rounds of strict quality inspection procedures before it can be officially put into storage and delivered.
In the whole process, any slight deviation is not allowed, because even an error of 1% mm may cause the final product to fail to meet the actual use requirements. Therefore, only when all inspection reports are in "PASS" status will they be packaged and sent to the customer.
Future Trends: Smart Grid and Automation Integration
With the advancement of science and technology, the future of low-voltage electrical terminals will also usher in new opportunities for change. On the one hand, the gradual improvement of the level of intelligence has prompted a new generation of products with more user-friendly features, such as built-in self-checking sensors that can provide early warning of possible problems, or equipped with remote data acquisition interfaces to facilitate centralized management and maintenance upgrades. On the other hand, with the increasing popularity of the concept of the Internet of Things, more and more traditional hardware will be integrated into wireless communication protocols to achieve interconnection.
At present, there have been many small distribution boxes with Bluetooth or Wi-Fi modules on the market. Users can view the load situation and historical statistical charts of each branch in real time through smart phone applications. I believe that in the near future, similar technologies will gradually penetrate into all kinds of terminal accessories, bringing more convenient experience and service value-added space for people.
Case Sharing: Successful Real-World Experience
Theoretical knowledge is important, but what really impresses people about something is often the practice that they have experienced. Next, let's take a look at several real examples of the successful use of low-voltage electrical terminals:
- urban rail transit construction project: during the expansion of the subway in a certain first-tier city, serious construction period delay was encountered. one of the important reasons was that the ventilation and exhaust pipe fans in the underground tunnel were caused by frequent power failure and restart, which led to excessive starting impact and burned down the motor windings. Later, the special custom-made quick plug-in aviation-grade sealed waterproof low-resistivity alloy contact finger was used as an alternative, which not only greatly reduced the probability of accidents, but also shortened the maintenance time by about 1/3.
- wind power station operation and maintenance optimization plan: offshore wind farms are facing the risk of salt spray erosion seriously threatening the deterioration and failure of lubricating grease in blade rotating bearings. therefore, a set of all-weather automatic fuel pump integrated with humidity sensing alarm and sound effect playback function is specially introduced
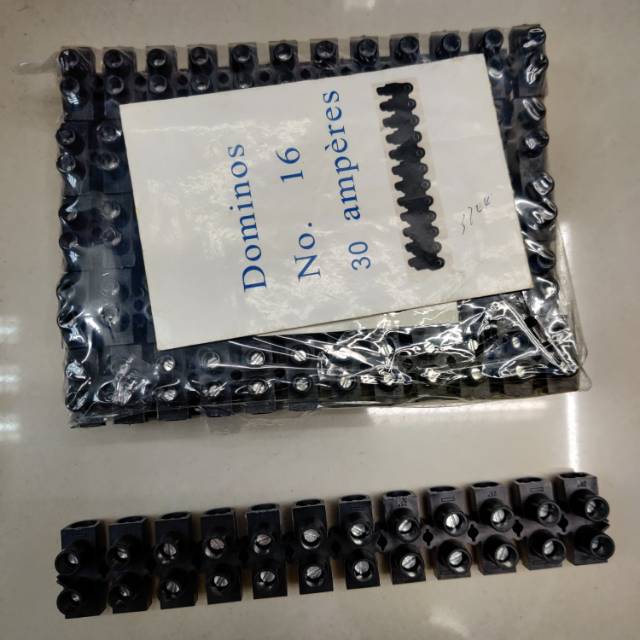