
In modern society, electrical equipment is everywhere, and stable power transmission is the basic guarantee for their normal operation. In this process, low-voltage electrical terminals play a vital role. Today we will delve into the functional characteristics of this key component and how to ensure the reliability of the system through correct selection and use.
Understanding Low-voltage Electrical Terminals: Analysis of Core Functions and Application Scenarios
Low-voltage electrical terminals are mainly used to achieve reliable connection between wires and cables, and to protect the line from the external environment. These small but extremely important parts are widely used in home distribution boxes, industrial control cabinets and other places where precise current management is required.
Materials and workmanship: the technology behind high-quality terminals
high quality low-voltage electrical terminals are made of copper with strong corrosion resistance and good electrical conductivity, combined with advanced surface treatment technology such as tin plating or zinc coating to enhance anti-aging ability. In addition there is an insulating plastic casing wrapped around the exterior for further improved safety.
This combination can not only withstand frequent plugging and unplugging operations within a high temperature range, but also maintain a good contact state for a long time to reduce the probability of heating caused by loosening.
How to select suitable low-voltage electrical terminals: size, current carrying capacity and other key parameters
In order to achieve the best results, before the purchase must be clear specific requirements including but not limited to the operating voltage level, the maximum allowable load and the required insertion aperture size and other factors to take into account. It is also necessary to pay attention to whether it has functional options such as dustproof and waterproof to adapt to more harsh working conditions.
Correct Installation Guide: Operating Steps to Avoid Potential Risks
even if you have the best product quality, if you do not follow the specifications, you will bury the signs of accidents. therefore, it is particularly important to follow professional guidance. First of all, the appearance of all parts should be carefully checked for defects, and then the assembly should be completed in accordance with the order indicated in the manual. Finally, the tightening degree of each part must be rechecked to confirm that there are no omissions before the power-on test.
FAQ: Analysis of doubts during terminal use
in response to some questions often raised by users, here are some simple replies. for example, when it is found that a certain interface has a spark, it is likely that the film formed by oxidation in the long-term exposure to air hinders the normal conduction. at this time, it only needs to be wiped clean gently and fixed again to restore the original state; if you encounter aging parts that are difficult to disassemble, do not force to avoid damage to the surrounding structure, but use special tools to assist in separation, which can save energy and better protect related facilities from damage.
In short, as long as you master the above points and adhere to regular maintenance, your system can always maintain efficient operation and benefit for a long time.
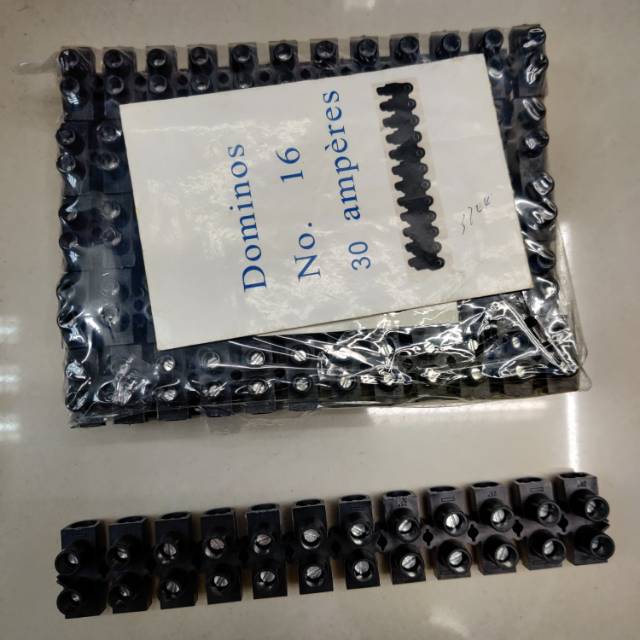